Basic vs Advanced Controllers and Beyond
The first step in choosing a chain hoist controller or designing a control system is understanding the range and capabilities of controllers that are available. The controller you choose should be dictated by the needs of the job.
These controllers, while limited in extra functions, are cheap, reliable, and well suited to basic hoist control systems. If you just need to control a limited number of hoists (1,2, 4 etc) and don’t need anything other than up/down and an E-Stop then basic controllers would suit the bill for you.
A simple rule is that you should only ever need 1 run button to control your hoists. If you find yourself needing 3 hands to run all the hoists on a job, then you need either a larger basic controller or an advanced controller.
Advanced controllers and systems will generally include the ability to link multiple controllers together so you can operate all the hoists together and allow for remote control interfaces so that you can control the hoists from a location where you can see everything.
Networkable or linkable controllers allow you to split into small systems e.g., 1 x 8 channel controller on one event and 1 x 12 way controller on another, and then later link two or more controllers together to control more hoists e.g. 1 x 8 channel + 1 x 12 channel for 20 hoists at once. Linked controllers should also include linked E-Stop circuits so that activating any E-Stop in the system will shut down all the hoists, not just that one controller.
Motion Control
Moving beyond the advanced control systems we get into the world of motion control. Motion control is generally, but not always, going to include load cell inputs for measuring overload and underload, encoders to allow accurate positioning and speed measurement, and sometimes variable speed drives to allow for multi-hoist synchronisation and selectable movement speeds. Motion control systems may be relatively simple systems or cue-based show control systems. The capabilities of the control system are generally very customisable and specific to a particular event requirement rather than off the shelf “All-in-one” systems.
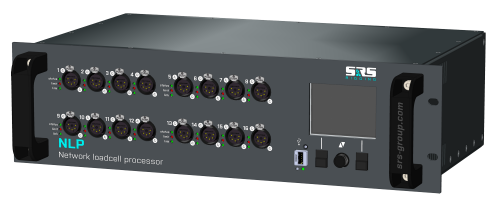
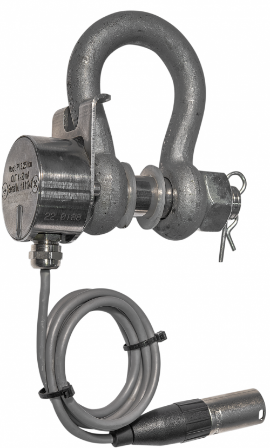
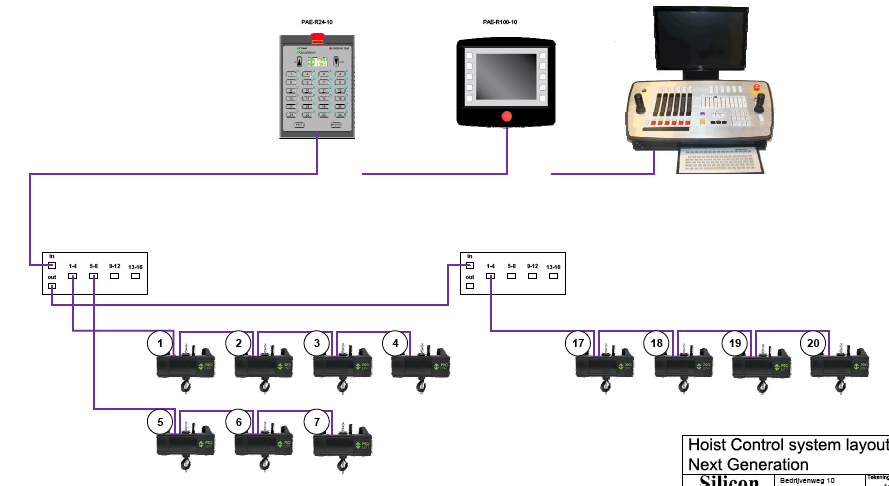
General operation guidelines
Carry out a risk assessment on the lifting operations you need to perform and choose a control system that is suitable for that job.
Ensure that the operator of a chain hoist control system is appropriately qualified. In Australia, this means a minimum of a Basic Rigger for single chain hoists or an Intermediate Rigger for multiple hoists.
Make sure that the operator of the hoist system can see the hoists that they are moving. Adding a remote-control unit can make this easier by letting the operator move into a position where they can see the hoists. If that isn’t possible, there should be a spotter in direct communication with the operator.
If you are using multiple controllers linked together, always ensure that activating one E-Stop shuts down all connected controllers/hoists.
If you are lifting close to the capacity of the hoists or doing complicated multi-point rigging, consider using load cells to monitor loads on individual hoists. Where possible, the loadcell system should integrate with the controllers to allow E-Stop activation if load limits are exceeded.
Check the correct movement of the hoists prior to lifting. If pressing Up doesn’t make the hoists go up then you need to correct the phase rotation at the controller.
Features | Basic | Advanced | Motion Control |
---|---|---|---|
Portable or Pendant form factor |
✓ |
✘ |
✘ |
Linkable/Networkable |
? |
✓ |
✓ |
Automatic Phase Reversal |
✘ |
? |
✓ |
Portable or Pendant form factor |
✘ |
? |
✓ |
Portable or Pendant form factor |
✘ |
✓ |
✓ |
Portable or Pendant form factor |
✘ |
? |
✓ |
Portable or Pendant form factor |
✘ |
✘ |
✓ |
Portable or Pendant form factor |
✘ |
✘ |
✓ |
? - Available on some units | ✘ - Typically not available | ✓ - Typically standard