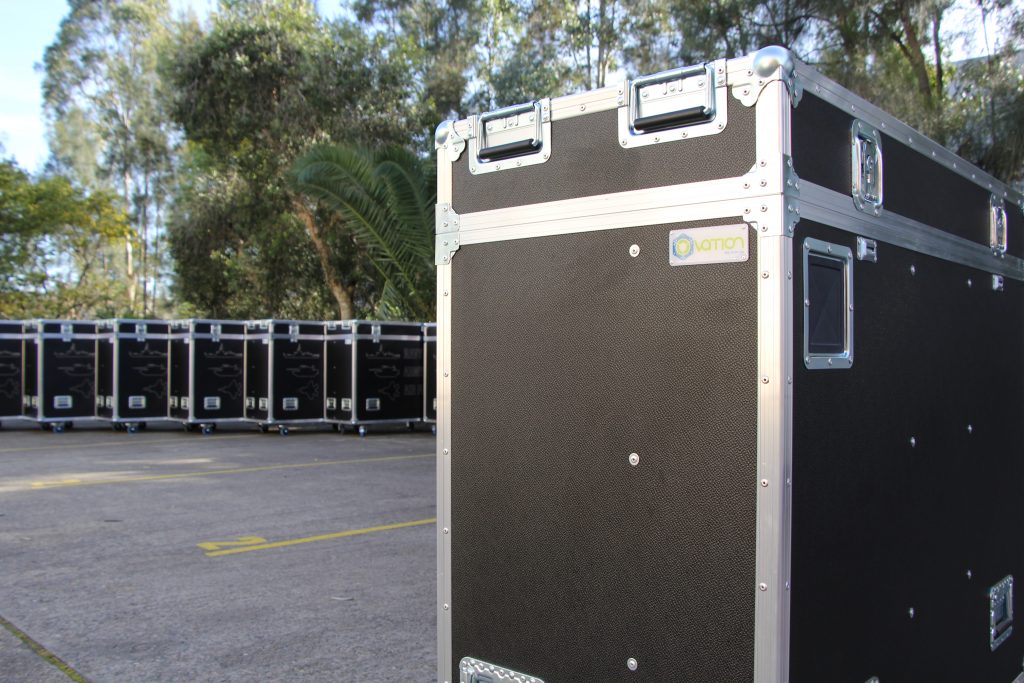
A Brief Introduction
The Design and Manufacturing team at Ovation are always striving for developing and manufacturing new road-case concepts to the market. One of the best examples of this is an extensive range of motorised screen lift cases. Unlike the traditional screen cases that are only used for transit of the screens, the new screen cases are equipped with an electric screen lift. This allows the screen to be stored and transferred inside the case, and once on site, deployed with the press of a button.
Considering their high quality and ease of use, the cases joined our best-selling designs very quickly. However, our team didn’t settle for ‘good’ and pushed the design to be the best. Engraved branding, integrated desktop surface, industry-standard power management, and internal storage were added to the design to make sure it ticks all the boxes.
In August 2022, we received an order for a large quantity of screen lift cases to be designed and manufactured with a very quick turnaround. We took this as a challenge to create all requested cases within the given deadline of just a few weeks. We accepted the challenge to design a case that would meet all requirements as we firmly believe in avoiding compromises. Having the best design and manufacturing team in the industry, a complete range of stocked material and hardware, more than 25 years of design knowledge, and local manufacturing facilities were the key factors in delivering this project.
The Solution
We started brainstorming on the most suitable type of protective screen case for our client’s order. As we have varying types of protective screen cases such as our Screen Cases with Motorised Electric Lift and Off-the-Shelf Screen Cases with Custom Fit-Out, we have years of experience on what to expect and its production.
Based on our client’s requirements, we found that one of our existing design, the Screen Cases with Slimline Motorised Lift, was the most suitable in what they were looking for. It features the following:
- Heavy-duty hardware and materials made by Adam Hall
- Slim electric lift with both fixed control panel and wireless remote
- Suitable for screens up to 75″ and 65kg in weight
- Table-top pieces to cover and dress the storage compartments while the screen is lifted
- Foam lined compartments for power management and accessories
- Customised EVA foam fit-out to protect the screen while in storage
- Cable glad dish with rubber diaphragms for routing power leads out of the case
- Swivel castors with reinforced steel backing plates
- Scandinavian birch plywood with protective PVC laminate and backing film
We chose this specific design as it does not only protect monitors and ensures efficient set-up times, but it is also designed with transit in mind with its attached trolley wheels. It ensures easy transportation from warehouse to warehouse, venue to venue, or to a different location altogether. Its structure ensures the easy and efficient movement of the case.
While these cases ensure the protection of the screen in-transit, the magic occurs when it arrives on site. Being equipped with a motorised lift decreases the necessary labour and time for setting up the monitory to the press of a button. It is essentially “ready for battle right out of the box”.
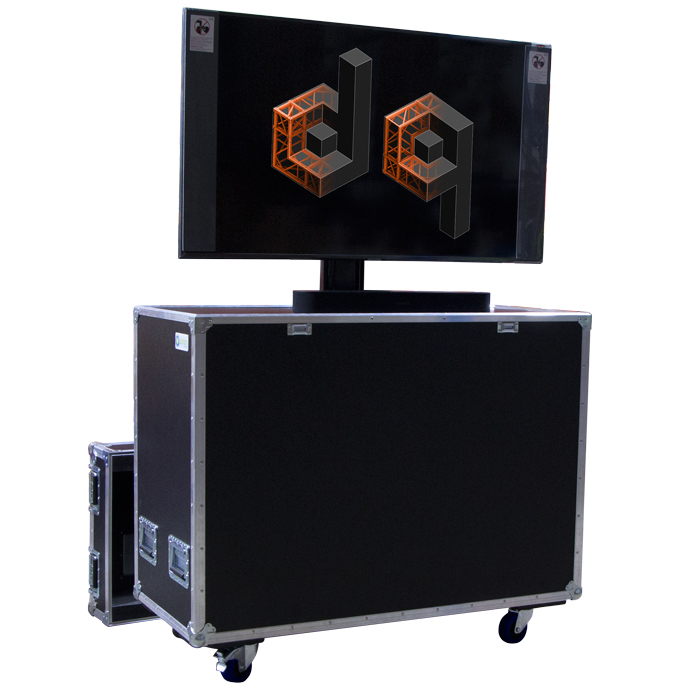
The Delivery
At Design Quintessence, we have more than 25 years of experience in designing industry-best solutions. Our in-house team of designers were able to quickly identify the best solutions for the given brief, draw all the custom components, and prepare the technical drawings for the production. Our cloud-based drawing system enables the clients to make sure all their requirements are met without leaving anything to chance.
Once the design was approved, our designers prepared the product specifications, technical drawings and machining instructions for the manufacturing team. An integrated system across sales, design and manufacturing ensures that all the team members are going by the same 3D drawings and information as the clients.
While we stock an extensive range of hardware and materials from the world’s best suppliers, the number of requested cases was more than the total number of available motorised lifts in the country. However, our team was able to secure and ship the hardware direction from a supplier in the United States of America.
Manufacturing the cases went ahead smoothly as our experienced team of builders have already made similar cases in the past. The standardised processes and quality control measures ensured that all team members product the same high-quality products. Our familiarity with the product enabled us to efficiently produce the cases before the deadline. Our operations staff palleted and wrapped the cases to be shipped to multiple locations as specified by the client.
Throughout the process, we realised that it was only successful due to the present teamwork and collaboration across departments.